Lorem ipsum dolor sit amet, consectetur adipiscing elit, sed do eiusmod tempor incididunt ut labore et dolore magna aliqua. Ut enim ad minim veniam, quis nostrud exercitation ullamco laboris nisi ut aliquip ex ea commodo consequat. Duis aute irure dolor in reprehenderit in voluptate velit esse cillum dolore eu fugiat nulla pariatur. Excepteur sint occaecat cupidatat non proident, sunt in culpa qui officia deserunt mollit anim id est laborum.
Paragraph type - Rich Text block UK OHS Lab Safety
Paragraph type - Link Lists
Lab Safety Resources
- Chemical Hygiene Plan
- Model Template for all UK Labs
- Chemical Hygiene Plan Appendices
- Resources and Links in Support of Lab Safety
- Lab Setup and Shutdown
- Resources for Departments and PIs to Guide Lab Setup and Shutdown
UK Chemical Hygiene Plan - Zipper
Each chapter is a 'panel' in the zipper.
Chapter 1
INTRODUCTION
Purpose
The purpose of this model Chemical Hygiene Plan is to define work practices and procedures to help ensure that Laboratory Workers at the University of Kentucky are protected from health and safety hazards associated with the hazardous chemicals with which they work.
Background
The Chemical Hygiene Plan is part of the University's compliance with the regulations promulgated on January 31,1990 by the U.S. Department of Labor Occupational Safety and Health Administration (OSHA) and adopted by Kentucky OSH. This standard entitled "Occupational Exposures to Hazardous Chemicals in Laboratories" is hereafter referred to as the Lab Standard. See Appendix I for information on obtaining or viewing a copy of the Lab Standard.
Overview
By OSHA regulations the Chemical Hygiene Plan must include:
- Standard Operating Procedures
- Criteria to determine and implement specific control measures, such as engineering controls and personal protective equipment
- An ongoing program to ensure that laboratory chemical hoods and other engineering controls are functioning properly
- Information and training requirements
- Circumstances under which a particular laboratory function will require "prior approval"
- Provisions for medical consultation and medical exams
- Designation of the Principal Investigator/Laboratory Supervisor as the Chemical Hygiene Officer
- Additional precautions for work with select carcinogens, reproductive toxins, and extremely toxic substances
- This model Chemical Hygiene Plan (referred to as the Plan throughout this document) will be reviewed annually by the institutional Chemical Hygiene Officer and/or the Chemical Safety Committee. Each laboratory's Chemical Hygiene Plan must be reviewed annually by the laboratory's Chemical Hygiene Officer and the "revised date" must be listed on the Plan. [For discussion of Institutional Chemical Hygiene Officer and Chemical Hygiene Officer see Chapter 9].
- All Laboratory Workers, prior to the commencement of lab duties, must read this Chemical Hygiene Plan. In addition to the Plan, the Laboratory Workers must be familiar with and adhere to prudent laboratory safety guidelines developed by their Laboratory Supervisor, UK requirements and other relevant regulatory requirements (e.g. Radiation Safety).
- A written record stating that each Laboratory Worker has reviewed the Chemical Hygiene Plan and related health and safety policies and guides must be kept by the CHO and available for review upon inspection. (See Form I for an example of a training record form.)
Definitions
Hazardous Chemical - OSHA has defined a hazardous chemical as "a chemical for which there is statistically significant evidence based on at least one study conducted in accordance with established scientific principles that acute or chronic health effects may occur in exposed employees".
Laboratory - OSHA defines a laboratory as "a workplace where relatively small quantities of hazardous chemicals are used on a non-production basis.”
Lab workers - are employees. OSHA defines an employee as "an individual employed in a laboratory workplace who may be exposed to hazardous chemicals in the course of his or her assignments." An example of a Laboratory Worker would be a University teaching assistant, research assistant or faculty member instructing an academic lab. OSHA would not consider students in an academic laboratory as employees. However, as a matter of university policy, the principles outlined in this Chemical Hygiene Plan will apply to students in our laboratories. Also included, will be visiting professors and volunteers that might be working in the lab. Thus, Laboratory Supervisors must ensure that these groups that are in their laboratories are adequately instructed in relation to safe laboratory procedures.
Minors in Research Laboratories or Animal Facilities
Students under the age of 18, not enrolled as a University of Kentucky student, who wishes to do research in a lab must follow the Minors in Research Lab Policy and accompanying forms. The policy can be found at the following website https://ehs.uky.edu/docs/pdf/ohs_minors_in_labs_0001.pdf.
Assistance
If there is any question about where the Lab Standard applies and whom it covers, the Occupational Health and Safety Department, upon request, will make this determination. The University of Kentucky office of Environmental Health and Safety has professionals in several disciplines (e.g. Radiation Safety; Environmental Management; Fire Marshal; Occupational Health/Industrial Hygiene & Safety) that can be consulted related to laboratory safety. See Appendix II for an organizational chart.
Chapter 2
RESPONSIBILITIES
Background
The University of Kentucky is committed to providing a safe and healthful environment for all persons associated with the institution. The University intends to be a role model for the Commonwealth in its environmental stewardship, health protection and safety standards and its compliance with all laws and regulations relating to the environment, health, and safety. Management, faculty, staff, and students are asked to support these goals in all university activities and the University administration will provide the necessary resources to achieve these goals.
A vast array of educational activities and research utilizing hazardous materials is conducted at the university that requires cooperation of all parties involved to ensure that such activities are conducted safely with regard to workers, students, the community, and the environment. The following outlines specific responsibilities associated with laboratory safety and this Chemical Hygiene Plan.
Faculty and Staff in charge of supervising laboratories (referred to as Laboratory Supervisors throughout document) have the following responsibilities for implementing the Chemical Hygiene Plan:
- Inform and train employees concerning chemical safety as required by this Plan. Retain training records and all documentation
- Implement and enforce rules and standards of this plan concerning health and safety for laboratories under the supervisor's jurisdiction and restrict access to the laboratory (see Authorized Access in Chapter 3 "Standard Operating Procedures")
- Serve as the "Chemical Hygiene Officer" for his/her laboratories
- Ensure compliance of Laboratory Workers with this Plan
- Ensure the availability and enforce the proper use of appropriate personal protective equipment and relevant health and safety reference materials
- Remain cognizant of chemicals stored and used in labs and their associated hazards
- Reconcile the laboratory’s chemical inventory, annually (see Appendix IV for sample inventory form)
- Conduct internal inspections of labs for health and safety concerns and maintain an inspection log of inspection findings (see Appendix III for a sample self-inspection form. Also visit the website for the example table of laboratory violations https://ehs.uky.edu/ohs/inspections.php.
- Request assistance from Environmental Health and Safety, as needed
- Request allocation of funds from superiors for health and safety improvements as needed, or budget into research grant proposals
Laboratory Worker responsibilities regarding implementation of the Chemical Hygiene Plan:
- Follow all health and safety standards and rules
- Report all hazardous conditions to the Laboratory Supervisor
- Wear or use prescribed protective equipment
- Report any suspected job-related injuries or illnesses to the Laboratory Supervisor and seek treatment immediately
- Refrain from the operation of any equipment or instrumentation without proper instruction and authorization
- Remain aware of the hazards of the chemicals in the lab and how to handle hazardous chemicals safely
- Request information and training when unsure how to handle a hazardous chemical or procedure
Deans, Directors, and Heads of Academic and Administrative Units have the primary responsibility for the health and safety of their staff and students. Specific responsibilities regarding the implementation of the Chemical Hygiene Plan include:
- Collaborate with faculty and staff to adapt the Model Chemical Hygiene Plan to include lab-specific guidelines and to develop strategies to implement the Plan.
- Consider the idea of developing departmental-wide laboratory safety training programs, committees, and shared use facilities.
- Make budget arrangements for health and safety improvements. It is the responsibility of these respective individuals to request the necessary monies in the budget process
Environmental Health and Safety Department responsibilities include the following:
- Appoint an Institutional Chemical Hygiene Officer who will routinely review the model Chemical Hygiene Plan and suggest modifications as needed
- Provide technical assistance to Laboratory Supervisors and workers concerning appropriate storage, handling, and disposal of hazardous chemicals
- Provide general laboratory safety training upon request
- Conduct exposure assessments and laboratory inspections upon request and on a routine basis
- Provide technical assistance concerning personal protective equipment and laboratory safety equipment; and
- Remain current on rules and regulations concerning chemicals used on campus.
Chapter 3
STANDARD OPERATING PROCEDURES
Purpose
The Lab Standard requires operating procedures relevant to safety and health considerations to be followed when laboratory work involves the use of hazardous chemicals. This Plan represents a minimum set of guidelines for UK laboratories handling hazardous chemicals.
Background
The Lab Standard is intentionally vague about SOPs. Individual administrative units, laboratories or research groups are required to develop more detailed procedures as the situation arises. These procedures must be written, added to the laboratory's Chemical Hygiene Plan, and made available to Laboratory Workers. To assist in the development of SOPs Form IV can be used. Acceptable lab safety references such as those listed in the OSHA Lab Standard may be adopted in whole or may be useful in developing additional procedures. In all situations, individual faculty or staff will be responsible for enforcing adequate safety and hygiene measures in laboratories they supervise. If necessary, additional assistance from Environmental Health and Safety is available.
Hierarchy of Defense
To protect workers from exposure to hazardous chemicals there is a hierarchy of defense. At the top of the hierarchy are engineering controls. Engineering controls consist of general room ventilation and most notably in laboratories, fume hoods. The second is work practice/administrative controls and finally, personal protective equipment (PPE). It is imperative that all lab personnel know what PPE is appropriate for all operations in the lab, what work practices are to be followed and then to understand how the engineering controls work.
The following standard operating procedures apply to all labs at the University. Your lab may require additional requirements as determined by a hazard evaluation.
Personal Protective Equipment
Attire Proper attire must be worn in the laboratory. All lab personnel must be wearing a lab coat when there is active work being done with hazardous materials such as biologicals, chemicals, radiologicals and physical hazards. Legs and feet must be covered, i.e. no open toed shoes. Legs must be covered to at least ankle length. Nylon hoses and tights are not considered appropriate attire. Loose clothing and long hair must be confined. Additionally, to enter the lab, eye protection must be worn. This includes all laboratory personnel as well as visitors. PPE must be left in the laboratories and not worn in public areas. Modification to this attire policy can be requested by contacting Occupational Health and Safety at 257-1376.
Eye Protection It is University of Kentucky policy that any University personnel including Students, Faculty, Staff and visitors shall wear appropriate safety glasses at all times when work is being conducted in the lab with hazardous materials as determined by the Assessment Chart and Hazardous Waste Identification Chart Index. The wearing of contact lenses in labs has been a controversial issue. Most research has shown there is no greater risk when wearing contact lenses. Contact your optometrist or ophthalmologist for additional questions.
Face Shields Full-face shields must be worn when conducting a procedure where splashing of corrosive or injurious material is a potential. Face shields must be worn when working with >4 liters of corrosive liquid. Full-face shields with bottom caps to protect under the chin are preferred due to the tendency to raise the chin when a splash occurs.
Footwear All footwear must cover the entire foot, be slip resistant and be made of impermeable material (e.g. leather). Perforated shoes do not provide adequate protection against spilled materials.
Gloves Most laboratories will require more than one type of glove material. Latex examination gloves are not meant to provide protection from chemicals and should not be used in labs for this purpose. Nitrile is a good all-purpose glove material and has less of an issue for allergic reactions. Appendix IV offers some generic information for glove selection. Your glove supplier can also provide information. When working with highly hazardous chemicals that can be absorbed through the skin, specific glove testing information should be obtained from the manufacturer. Written information needs to be provided to all lab workers preferably in the form of an SOP, Form IV. Occupational Health and Safety (257-2924) can provide additional assistance in appropriate selection.
Gloves shall not be worn in halls or public areas. When samples are transferred through general use areas, a secondary container is recommended. If a sample must be carried by hand, glove one hand to hold a protected sample. The ungloved hand shall be used to open doors or push elevator buttons. In the lab be aware of using common equipment with gloved hands such as computers and phones.
Lab Coats and Aprons
The primary purpose of a lab coat is to protect against splashes and spills. A lab coat shall be nonflammable, where necessary. A lab coat should fit properly and should be easily removed. Lab coats shall be buttoned when in use. Lab coats shall be clean. If a coat becomes contaminated remove immediately. Lab coats shall never be taken home to be laundered. A lab coat can be laundered in a work-related on-site washer and dryer. Also, a laundry service, typically handled by the department, can be used. Contact your supervisor if you have questions.
If working with flammable materials, such as pyrophorics, a flame-resistant lab coat is required.
Rubber coated aprons may be needed for work with corrosive chemicals, depending on the specific tasks to be done.
The chart below can help establish the appropriate lab coat needed in the lab.
Task |
Material Needed |
General Lab Work |
100% Cotton Lab coat |
>4 Liters of Corrosive Material |
Rubber Coated apron |
Pyrophoric Materials |
Flame resistant lab coat |
Respiratory Protection
The use of some substances may require respirators. See Chapter 4 for a discussion of "Controlling Chemical Exposures". Any use of respiratory protection in the lab requires prior approval from OHS. Please contact the Institutional Chemical Hygiene Officer.
HAZARD ASSESSMENT AND PERSONAL PROTECTIVE EQUIPMENT REQUIREMENTS FOR GENERAL LABORATORY OPERATIONS
Hazard |
Personal Protective Equipment Required
|
|
||
|
Eye |
Face |
Hand/Skin/ Body |
|
Any laboratory use of chemicals |
Safety glasses always |
|
Lab coat |
|
Use of corrosive chemicals, strong oxidizing agents, carcinogens, mutagens, etc.
|
Chemical splash goggles |
Full face shield and goggles (for work with >4 liters of corrosive liquids) |
Resistant gloves (See Appendix VI for chemical resistance of common glove materials)
Impervious lab coat, coveralls, apron, protective suit (for work with >4 liters corrosive liquids) |
|
Temperature extremes |
Safety glasses always |
|
Insulated gloves for handling ovens, furnaces, cryogenic baths, and other devices over 100° C or below -1° C |
|
Sharp objects (broken glass, insertion of tubes or rods into stoppers) |
Safety glasses always |
|
Heavy cloth barrier or leather gloves |
|
Work Practice and Administrative Controls
Authorized Access The laboratory supervisor must restrict access to laboratories. If the lab is not attended the entry door should be locked. Children (under age 17) are not allowed in laboratories except as authorized by the laboratory supervisor for an officially sanctioned activity (e.g. class or open house). Pets are also prohibited from laboratories.
Broken Glassware Broken glassware cannot be disposed of in the regular garbage. It should be placed in a box with a plastic liner so that no shards can present a hazard when disposing of the entire container. Do not overfill the container; keep it under 30 pounds.
Chemical Handling Encourage the use of poly coated bottles or use bottle carriers for transporting chemicals that are in regular glass containers. Close caps securely and avoid storing chemical containers in hard to reach areas. Pour chemicals carefully, and never add water to concentrated acid. Metal containers and non-conductive containers (e.g., glass or plastic) holding more than five gallons must be grounded when transferring flammable liquids.
Chemical Inventory An annual updated chemical inventory is required for all laboratories on campus. The University is using the Chematix Chemical Management Software system. Please see Form II for more information. For questions please notify Robert Thomas 257-4016.
Chemical Spills and Accident Response As a matter of policy, University personnel should handle their own small spills and releases. For emergency situations i.e., large spills and leaks, evacuate and call 911 (Campus Police) from a safe location. See Chapter 11, Planning for Emergencies for more information.
Chemical Storage A chemical is considered to be in storage when the chemical is not in active use. A chemical in storage should be stored in appropriate container such as a glass or plastic container with a secure tight-fitting lid. Round bottom flasks are not considered proper storage containers. Parafilm and aluminum foil are not considered to be secure lids.
Chemicals should be stored by compatibility, not simply by alphabetical arrangement. Oxidizers should be separated from organics, air/water reactives must be kept dry and cyanides should be stored away from acids. (See Appendix V for examples of incompatible chemicals).
Flammable liquids including hazardous waste shall be limited to 10 gallons per 100 ft2. Half that amount must be in a flammable storage cabinet. Please review fact sheet at https://ehs.uky.edu/fire/flstpol1.html.
Cold Storage of flammables in a refrigerator are prohibited unless it is approved for such storage. Such refrigerators are designed not to spark inside the refrigerator. If refrigerated storage is needed, choose either a flammable safe or explosion proof refrigerator. More information about the different types of refrigerators can be found at the following web page, https://ehs.uky.edu/docs/pdf/ohs_refrigerators.pdf.
Peroxide forming chemicals shall be labeled when received and opened, then disposed of by the manufacturer’s recommendation or within a specified time as discussed here: https://www.as.uky.edu/sites/default/files/Peroxide%20Former%20Guideline_0.pdf .
Containers Check the integrity of containers and if damaged or leaking, transfer to an acceptable container or call Environmental Management for assistance (323-6280). For disposal, complete an E-Trax waste pickup request and submit to Environmental Management. Observe chemical compatibility; for example, hydrofluoric acid must not be stored in glass and some oxidizers should not be stored in plastic containers.
Cylinder Handling and Storage: https://ehs.uky.edu/ohs/cgc2.html
General Transport of Cylinders
- Transport cylinders by hand truck, do not roll, drag, or slide cylinder
- Secure cylinder to hand cart
- Move cylinders with valve caps in place
- Move extremely toxic chemicals (e.g. hydrogen sulfide, chlorine, and arsine) during off hours if possible
General Storage of Cylinders
- Secure cylinders to a wall or immovable object always
- Secure cylinders upright, with either a valve cap or gauge on the cylinder
- Store cylinders in a well-ventilated area
- Separate empty and full cylinders
- Secure cylinders according to compatibilities
General Use of Cylinders
- Match regulator with the cylinder
- Use the appropriate tubing
- Use appropriate PPE when needed
Other Considerations
- Contact manufacture for information on use and compatible materials
- Cylinders must be added to UK’s chemical inventory system, Chematix: https://etrax.chematix.com/Chematix/more details on page 112)
- For storage and use of flammable gasses, contact the Fire Marshal, 257-6326.
Disposal of Waste It is important to segregate waste. To request pickup of hazardous, biohazardous or chemical waste, call Environmental Management at 323-6280 or complete an E-Trax waste pickup request (https://etrax.chematix.com/Chematix/). Disposal of all laboratory waste must follow the procedures specified by Environmental Management: https://ehs.uky.edu/env/waste_management.php. To request pickup of radioactive wastes, contact Radiation Safety at 323-6780.
The Hazardous Waste Contingency Plan is a useful reference guide regarding Hazardous Waste Contingency Plan areas that accumulate hazardous waste (Satellite Accumulation Areas (SAA’s). This plan also outlines Emergency Action Plans (BEAP) involving hazardous waste: https://ehs.uky.edu/env/media/contingency-plan-quick-reference-guide.pdf.
Door View Panel Laboratory door view panel should not be covered.
Electrical Policy Extension cords shall not be used as permanent wiring. Only Underwriters Laboratory (UL) listed surge protectors that are ground and have a built-in 15-amp circuit may be used. For more information regarding UK’s Electrical Policy: https://ehs.uky.edu/fire/electrical.html.
Equipment Use proper equipment that is in good condition. For example, never use chipped or cracked glassware. Never modify electrical equipment outside of the manufacturer’s specification. Use flammables with only approved equipment such as blenders. Flammables that require cooler temperatures for storage should be put in specific refrigerators/freezers. One is referred to as flammable safe and has no exposed ignition sources inside the cabinet, such as lights or switches that could ignite vapors. These are less expensive than the explosion-proof refrigerators/freezers and would be adequate in most lab applications. The other type of refrigerator/freezer is referred to as explosion-proof. This type may be required in rare circumstances for hazardous locations. Explosion-proof or spark-proof units have no interior or exterior ignition sources and are considerably more expensive. For more information on selection of a flammable safe or explosion proof refrigerator, refer to the Cold Storage section on the previous page.
Food, Drink, Cosmetics Eating, drinking and the application of cosmetics (including lip balm) are forbidden in areas where hazardous chemicals, biohazards and radioactive materials are used. These activities must be in designated, well defined non-chemical areas that are separated from the lab area by physical barriers such as partitions or filing cabinets. A line on the floor will not be considered adequate separation. Consumables must not be placed in the same refrigerator as chemicals, biohazards, or radioactive material.
Glass Tubing When inserting tubing into stoppers, lubricating tubing as well as wearing gloves or wrapping in a thick cloth will help to protect hands from being cut in the event of the tubing slipping and breaking.
Hazardous Materials Hazardous materials should not be used on open laboratory benches.
Headphones/Earphones These listening devices are acceptable as long as the volume is not too loud. The wearer of these devices must have the volume low enough so that they are able to carry out a normal conversation. Normal laboratory operations as well as alarms, (fume hood, fire, etc.) should be heard when the listening devices are in use.
Horseplay Practical jokes or other inappropriate and unprofessional behavior in the laboratory setting is forbidden. Avoid distracting or startling any other workers.
Housekeeping Exits, aisles and safety equipment must NOT be obstructed in any way with equipment, furniture, etc. No items can be stored in the corridors. For questions related to the use of corridors, exits, or other Fire Marshal issues, contact the Fire Marshal’s office (257-6326).
Labeling All chemical containers must be labeled. All labels must be legible, in English and include chemical/product name (chemical formulas alone are not acceptable) and relevant hazards. Labels on incoming containers must not be removed or defaced. Peroxide forming chemicals shall be labeled when received and opened, then disposed of by the manufacturer’s recommendation, or within a specified time as discussed here: https://www.as.uky.edu/sites/default/files/Peroxide%20Former%20Guideline_0.pdf.
Waste chemical containers must be clearly marked as “Hazardous Waste” indicating the specific name of the waste chemical(s), rough percentage(s), and hazard class (e.g., flammables, oxidizers, carcinogen, etc.). Contact OHS or Environmental Management for hazardous waste labels. Do not date waste containers until they are full and ready for pickup.
Reaction intermediates should be labeled. These chemicals shall be assumed as hazardous and subject to the Chemical Hygiene Plan. To ensure compliance, label the container with as much information as possible such as parent compounds, any potential hazards and health effects.
LABORATORY DOOR SIGN Each laboratory door must be legibly marked with the following information:
1. Room number
2. Department
3. Laboratory Supervisor's name
4. Emergency contacts, including names, office location, and office and emergency telephone numbers
5. Special hazards/instructions (e.g. location of large quantities of flammables or the presence of a "local alarm" system)
Use the Bioraft Door Sign Function to create your LABORATORY DOOR SIGN
Mercaptans To avoid false reporting of natural gas leaks, the Physical Plant department should be contacted when mercaptans are used in a laboratory in such a manner that persons outside of the laboratory could smell the mercaptan and suspect a natural gas leak in the building. Please review the fact sheet at https://ehs.uky.edu/docs/pdf/ohs_mercaptans.pdf If a natural gas leak occurs, the building should be evacuated, and the proper authorities should be notified. For more information about the emergency response procedures for natural gas, please view the following website: https://ehs.uky.edu/fire/natgas.html.
Mouth Pipetting Mouth pipetting is forbidden.
No Smoking This policy exists throughout the University and applies in all laboratories.
Open Flames on Benchtop Whenever possible, open flames should be replaced by electrical heating. Prior approval is needed if open flames are to be used in the laboratory.
Open Lab Designs When working in an open lab design, such as the Biomedical Biological Sciences Research Building (BBSRB), noise should be kept to a minimum. Be aware that neighbors cannot simply close the lab door to reduce the noise. Sound attenuating devices should be used for noise producing bench top equipment, such as sonicators.
Pregnant Laboratory Workers If a worker is pregnant or is planning to become pregnant, (OHS) can provide guidance for working with reproductive toxins. More information can be found at the following website: https://ehs.uky.edu/ohs/pregnant.php.
Perchloric Acid Contact OHS at 257-3242 for prior approval before initiating work with perchloric acid heated above ambient temperature or above 72% concentrations. It will give off vapors that can condense and form explosive perchlorates. Hence, when heating perchloric acid above ambient temperature, a specifically designed and dedicated perchloric acid Laboratory chemical hood with a wash down system or a local scrubbing or trapping system must be used.
Personal Hygiene Hands should be washed frequently throughout the day, before leaving the lab, after contact with any hazardous material, and before eating, drinking, smoking, and applying make-up or lip balm.
Personal Use of Chemicals Laboratory workers are not allowed to remove chemicals from the lab for personal use.
Piranha Solution Contact OHS at 257-3242 for prior approval before initiating work with Piranha Solution. Waste containers for Piranha Solution must be closed with a vented cap. Caps can be obtained from Environmental Management.
Pyrophoric/Water Reactive Chemicals
Special precautions need to be made when working with these compounds. A written standard operating procedure (SOP) must be done when any of these chemicals are used in the laboratory.
Recapping of Needles Recapping of hypodermic needles is prohibited in the laboratory. If recapping is required, contact OHS for prior approval.
Unattended Experiments Frequently, laboratory operations are carried out continuously or overnight. For experiments involving hazardous operations, it is essential to plan for interruptions in utility services such as electricity, water, and inert gas. Operations are to be safe and plans made to avoid hazards in case of failure. If necessary, arrangements for routine inspection of the operation can be made and, in all cases, the laboratory lights should be left on and an appropriate sign posted on the door.
Vacuum pumps and vacuum lines Exhaust from vacuums shall be vented through the fume hood or equipped with local exhaust. Vacuum lines leading from an experimental procedure shall always be equipped with traps to prevent contamination of vacuum equipment or house lines. Traps shall be evaluated for appropriateness and special safety precautions instituted if needed.
- Particulates: determine size range being generated and choose capable filtration
- Aqueous non-volatile: in most cases a filter flask at room temperature will prevent liquids from contaminating a vacuum source
- Solvent or other volatile liquids: choose a cold trap that is large enough and cold enough to condense vapors plus a filter flask large enough to hold all possible liquids that could be aspirated. Avoid using liquid nitrogen if possible. Liquid nitrogen should only be used in sealed or evacuated equipment and with extreme caution. Liquid oxygen can form if proper procedures are not followed. For most applications, a slurry of dry ice and isopropanol or ethanol can be used.
- Corrosive, highly reactive or toxic gases: a sorbent canister or scrubber shall be used that can trap the contaminant.
Waste Anesthetic Gas (WAG) Make sure that proper procedures are followed when using vaporizers and scavenging systems during animal surgeries. A fact sheet regarding safe use of Isoflurane can be found here: https://research.uga.edu/docs/policies/compliance/oacu/UGA-IACUC-Isoflurane-Guidelines.pdf.
Working Alone When working with acutely hazardous materials, it is advisable to have a second person present, or at a minimum, maintain surveillance via telephone contact.
Engineering Controls
Laboratory Chemical Hood and Other Engineering Controls See Chapter 5, “Laboratory Chemical Hoods and Other Engineering Controls.”
Safety Shower/Eyewashes Safety showers and/or eyewashes are required in labs where corrosive chemicals are used. PPD is charged with testing the eyewashes and shower units. A log of those checks can be obtained by contacting PPD.
Laboratory personnel should be familiar with using an eyewash or safety shower. Training for proper use can be found at the following website: https://ehs.uky.edu/classes/classes_ohs_0001.php#emergency_eyewash.
If operations in the lab require safety procedures greater than what is outlined above, please insert or reference the location of lab specific SOPs here. For the SOP template consult Form IV.
Chapter 4
CONTROLLING CHEMICAL EXPOSURES
The Lab Standard requires the employer to determine and implement control measures to reduce employee exposure to hazardous chemicals; particular attention must be given to the selection of control measures for chemicals that are known to be extremely hazardous. There are three major routes of entry for a chemical to enter the body: inhalation, absorption, and ingestion. Three types of controls for prevention of these various routes of entry include engineering controls, personal protective equipment, and administrative controls. Each route of entry can be controlled in several ways, as explained below.
Inhalation Hazards
Inhalation of chemicals is the most common route of entry. To avoid inhalation exposures, hazard reduction methods such as substituting a less volatile or a less toxic chemical or substituting a liquid or solid chemical for a gaseous one is the best means of control. If substitution is not practical, engineering controls such as ventilation should be used to lessen the chance of exposure. The use of well-functioning local exhaust ventilation such as laboratory chemical hoods, biological safety cabinets, vented glove boxes and other local exhaust systems is often required to minimize exposure to hazardous chemicals. Dilution ventilation may be used to reduce exposure to nonhazardous nuisance odors. For extremely toxic chemicals such as those classified as poisonous gases by State or Federal agencies (e.g., arsine, phosgene), the use of closed systems, vented gas cabinets, fail-safe scrubbing, detection or other stricter controls may be required and would require prior approval.
If both substitution and engineering controls are unavailable, the use of personal protective equipment may be required to reduce inhalation exposures. Respiratory protection from dust masks to self-contained breathing apparatus may be utilized to this end. If laboratory employees wear respirators, requirements of the OSHA Respirator Standard (1910.134) must be met and a written respirator program must be implemented. A respiratory program can be developed at https://ehs.uky.edu/ohs/respgate.php. This Standard requires training on the proper use of respirators; medical surveillance to ensure the user can wear a respirator, and fit testing to ensure that the respirator fits properly. A lab worker or his/her supervisor should contact the Occupational Health and Safety Department (257-3827) if respiratory protection is to be utilized to control exposures to hazardous chemicals.
In addition, the following principles should be utilized to reduce the risk of exposure to hazardous chemicals:
- Minimization of exposure time for individual employees
- Restricted access to an area where a hazardous chemical is used; and
- Proper signage on lab doors to indicate special hazards within.
Skin/Eye Contact Hazards
To reduce the risk of a chemical entering the body via skin and eye contact, use engineering controls such as substitution and appropriate ventilation as described above in Inhalation Hazards. The more obvious means of preventing skin and eye contact is the wearing of personal protective equipment such as eye protection, face shields, gloves, appropriate clothing (long pants) and shoes, lab aprons, lab coats, and other protective equipment as appropriate to the hazard. Since the chemical resistivity of the different types of protective equipment varies significantly, the lab supervisor should consult Appendix IV or other references to ascertain that the protective equipment material is resistant to the chemical being protected against. Safety showers/eye wash equipment is required where corrosive chemicals are used. Such equipment should be prominently labeled and not obstructed.
Ingestion Hazards
Ingestion of chemicals is the least common route of entry into the body. However a Laboratory Worker can easily ingest chemicals into the body via contaminated hands if they are not washed prior to eating, smoking or sticking part of the hand, or a writing tool that has been in contaminated hands, into the mouth. Some controls for preventing this route of exposure include engineering controls like isolating the hazardous substance so minimal contact is required (e.g., use glove box). Also, administrative controls such as forbidding mouth pipetting, encouraging good personal hygiene and designating a well-marked nonchemical area where eating, drinking and the application of cosmetics is permitted. And finally, personal protective equipment such as the wearing of gloves can reduce this type of exposure.
Exposure Assessment
At the request of faculty, staff or students, exposure evaluations may be conducted by OHS. Records of exposure evaluations will be kept in the Occupational Health and Safety Department and provided to the department and affected employees and any other appropriate authorities at the University. The following is a list of chemicals that require initial monitoring to determine exposures:
- Asbestos
- Vinyl chloride
- Inorganic arsenic
- Lead
- Cadmium
- Benzene
- Cotton dust
- 1,2-Dibromo-3-chloropropane
- Acrylonitrile
- Ethylene oxide
- Formaldehyde
- Methylenedianiline
- 1,3-Butadiene
- Methylene chloride
If you are using these chemicals in a process outside a fume hood, please contact OHS at 257-2924.
Flexy Grid
Body
Our Mission
The mission of UK Health & Safety is to provide a safe and healthful campus for employees, students, and visitors to work and study. This requires more than just complying with regulations and guidelines. The programs, audits and activities that OHS staff members engage in are all part of an overall system designed to help prevent injuries and illnesses: anticipation, recognition, evaluation, and control.
CTA
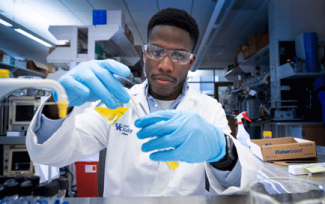
Potion #9
WWST
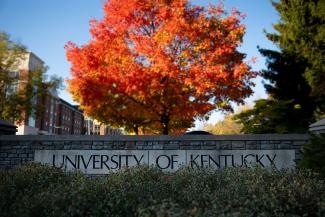
UK in the Fall
UK PR